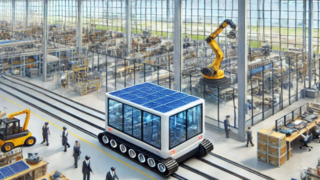
【要約】
こちらの記事は『生産設備の非固定化は製造現場に何をもたらすのか 導入事例から振り返る』の要約です。
導入事例
1. ヤマハ発動機:AGVバイパス方式による柔軟なライン運用
- 背景と課題
二輪車の国内生産台数は1980年代に600万台以上のピークを迎えた後、近年は70万台程度に減少。しかし、スポーツ系やオフロード系など、顧客ニーズに対応するための多様なモデルの生産が求められていました。季節需要やモデルごとの生産頻度の違いが原因で、従来の固定化された組み立てラインの稼働率にばらつきが生じていました。 - 解決策と成果
AGVの上に二輪車を載せて組み立てを行う「AGVバイパス方式」を導入。モデルに応じてAGVが経路を変更し、ライン長を模擬的に調整。これにより以下の効果を実現しました:- 生産ロットの縮小:1モデルあたりのロット数を従来の10分の1(4台)に削減。
- 稼働率向上:全モデルを効率的に生産可能に。
- 市場対応力の向上:季節需要や少量生産モデルにも柔軟に対応。
- ポイント
生産設備の柔軟性が、効率的で迅速な生産体制を支えています。
2. DMG森精機:AMRによる工程集約と無人化
- 背景と課題
ボールねじ加工では従来、5種類の機械を使い、各工程ごとに作業員がワークの出し入れや測定を行っていました。このプロセスは手間がかかり、リードタイムが長くなる要因となっていました。 - 導入したシステム
自社開発のAMR(自律型搬送ロボット)「WH-AMR 10」を活用。以下の特徴を持つシステムを導入:- 3次元ビジョンセンサー:ワークの位置認識や加工機のマーカーを読み取り、精密な動作を実現。
- 自動ハンド交換:さまざまなワーク形状に対応。
- 効果
- 人手作業を無人化。
- 特殊仕様の複合加工機と連携し、工程集約を実現。
- リードタイム短縮:効率化が進み、生産性が向上。
3. シチズンマシナリー:1個流しでリードタイムを大幅短縮
- 背景と課題
工程間のワーク移動は手作業で行われ、1バッチ(20~30個)の加工が全て終わらないと次の工程に進めませんでした。このため製品単位のリードタイムが長くなり、即時対応が難しいという課題がありました。 - 解決策
新工場でAMR(自律型搬送ロボット)「WH-MAR10」を導入し、以下の改善を実現:- 1個流し生産:各工程をリアルタイムで進行。
- 高温作業のロボット化:熱せられたスピンドルの焼きばめ作業も自動化。
- 成果
- リードタイムを従来の1/8に短縮。
- 安全性と効率性が向上。
4. 山善と東邦工業:協働ロボットとAMRの柔軟な分離運用
- 概要
「ROBO-COTATZ」は、協働ロボットとAMR(自律型搬送ロボット)を分離したモビリティシステム。AMRがロボットを作業場所に運んだ後、自身も搬送業務に従事可能な柔軟な仕組みです。 - 効果
- 1台のAMRで複数の協働ロボットをカバー。
- 故障リスクの分散。
- モジュール型運用により、柔軟な生産対応を実現。
その他の取り組み:NEDOの無線通信ガイドライン
- 概要
NEDOが策定した「製造現場における無線通信技術の導入ガイドライン」は、5G技術の活用を通じた柔軟な生産ライン構築を支援。 - 目指す成果
- IT/OTのデータ連携を通じて工場全体の最適化を実現。
- 生産ラインの迅速な組み換えが可能に。
まとめ
生産設備の非固定化は、製造現場に柔軟性と効率性をもたらし、多様化する市場ニーズや環境変化への即応を可能にします。AGVやAMRなどの導入事例は、効率化だけでなく、より持続可能で安全な生産システムの構築を示唆しています。これらの取り組みは今後の製造業の方向性を象徴するものといえます。
更に詳しい記事を読みたい方はこちら
【所感】
・AGV(無人搬送車)やAMR(自律型搬送ロボット)を用いた柔軟性のある製造現場が今後のトレンドになると感じた。
・製造業においてデジタル技術や自動化技術を使わず現状維持のままの企業はいずれ淘汰されると思う。
これらの本はKindle unlimitedで無料で読めます。※初回30日間は無料です
