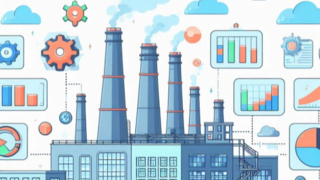
【要約】
こちらの記事は『データ収集からの可視化で終わりがちな工場DX、どうすれば先に進めるのか』の要約です。
1. 工場DXの現状と課題
工場DXは約10年にわたり推進されてきたが、データ収集や可視化までは進んでいるものの、そこから先のデータ利活用に進めている事例は少ない。
原因として、以下の点が挙げられています。
- 業務や組織間の“見えない壁”によるデータの分断
- トップダウン型DX施策による現場との温度差
2. HDSMの概要
これらの課題を解決するために日立が提案するのがHitachi Digital Solution for Manufacturing(HDSM)です。
HDSMは、日立の製造業での知見をアセット化したDXソリューションの総称で、次の3つの要素で構成されています。
- IoT基盤:多様な設備やシステムからデータを収集・蓄積
- アプリケーション群:データの可視化や分析を行うツール
- サポート体制:構想策定から運用までの伴走支援
3. IoT基盤の特長
IoT基盤では、製造業の4Mデータ(huMan、人 / Machine、設備 / Material、材料 / Method、方法)をひも付けたデータモデルを定義。
これにより、データの統合管理が可能となり、工程ごとに分断されたデータのサイロ化解消に貢献します。
また、クラウド環境を利用したIoT基盤クラウドサービス(IPCS)を提供し、最短1~2カ月でシステムの立ち上げが可能です。
4. アプリケーション群のラインアップ
HDSMでは以下のようなアプリケーションを用意し、現場の課題と経営課題を同時に解決します。
- 経営製造ダッシュボード:KPIと4Mデータをひも付けた経営分析
- 個体トレーサビリティ:製品の製造履歴追跡
- チェーントレーサビリティ:サプライチェーン全体の追跡
- 良品化条件シミュレーション:不良品発生の要因分析と品質安定化
- 電子帳票:紙帳票の電子化による効率化
5. サポート体制
工場DXの構想策定から稼働後の業務改革まで一貫支援する体制を提供。
企業ごとの要件に合わせたデータモデルの定義や、現場と経営をつなぐ仕組みの導入をサポートします。
6. 成功事例(サントリー食品)
サントリー食品では、原材料入荷から製造・物流・倉庫保管までの情報が分断されていたため、品質問題発生時の影響範囲調査に膨大な時間がかかっていました。
HDSMのチェーントレーサビリティを導入した結果、約360拠点の情報を一元管理できるようになり、
リスクの未然防止や迅速な影響範囲特定が実現しました。
7. 今後の展望
今後はHDSMにCO2排出量のトレーサビリティ機能を組み込み、カーボンニュートラルの取り組み支援にも対応する予定。
製造業の持続可能な成長を支えるソリューションとして、さらなる発展を目指しています。
更に詳しい記事を読みたい方はこちら
これらの本はKindle unlimitedで無料で読めます。※初回30日間は無料です
